From Selection to Implementation:
A Guide to Pick the Right WMS and TMS for Your Business

Written By
Arun Dev Kumar,
Manager – Supply Chain Solutions & Products.
23rd October 2024
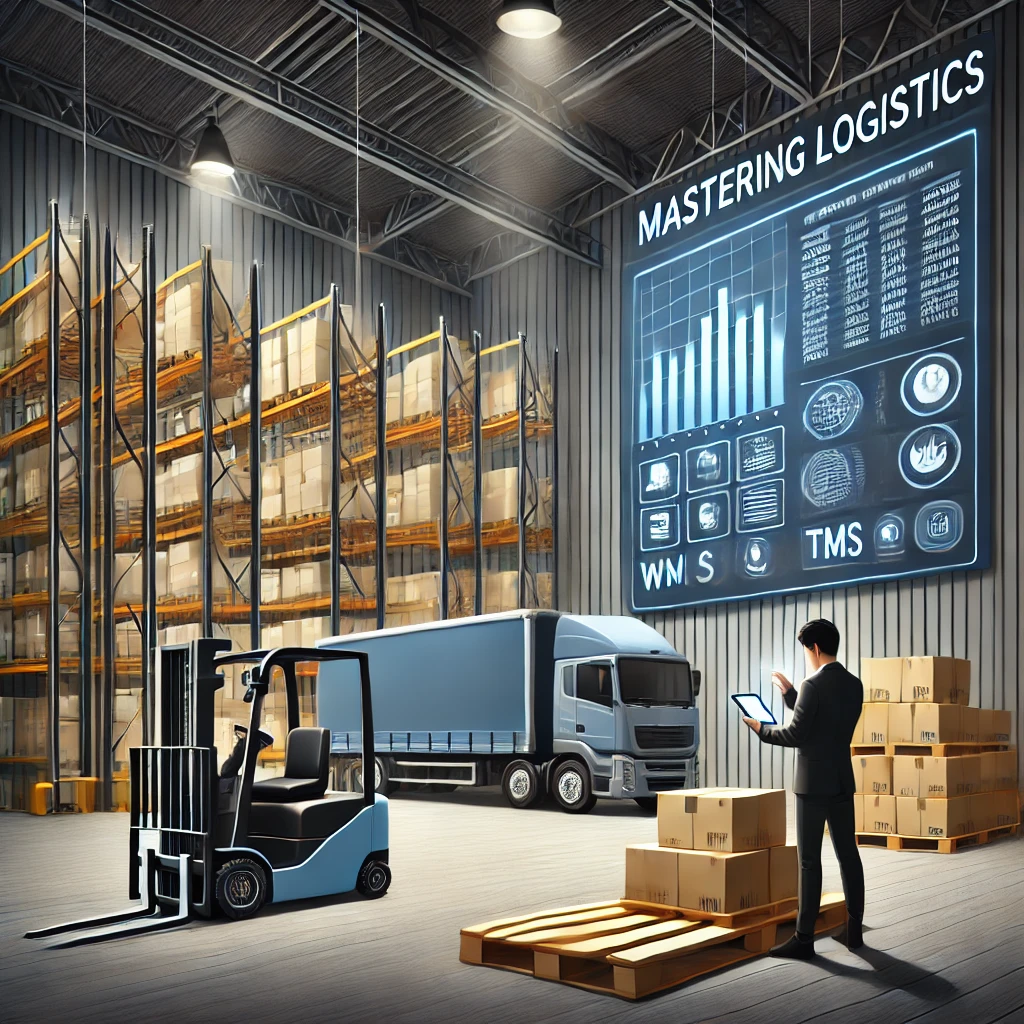
Selecting the right Warehouse Management System (WMS) and Transportation Management System (TMS) is essential for organizations aiming to optimize their logistics operations and gain a competitive edge. With a wide array of solutions available, ranging from established Gartner or Forrester leaders like SAP, Blue Yonder (BY), and Infor to tier-2 and tier-3 solutions or even custom in-house systems, the decision requires careful evaluation of various factors. This blog outlines the key considerations, industry trends, integration approaches, and best practices for selecting and implementing WMS and TMS solutions effectively.
Key Considerations for WMS and TMS Selection:
- Functional Requirements
- WMS Requirements: Look for essential functionalities such as inventory tracking, order fulfillment, automated replenishment, and cycle counting. Advanced capabilities, such as dynamic slotting, voice-directed picking, and integration with Internet of Things (IoT) devices for temperature or humidity monitoring, are crucial for industries like healthcare, food and beverage, and high-tech manufacturing.
- TMS Requirements: Must-have features include route planning, multi-stop routing, load optimization, carrier selection, and real-time shipment tracking. For complex logistics networks, support for multi-modal transportation and dynamic rerouting based on real-time conditions (traffic, weather) is highly beneficial.
- Vendor Tier Selection
- Top-Tier Solutions (e.g., SAP, Blue Yonder, Infor): These vendors offer comprehensive, integrated platforms with advanced functionalities, making them suitable for large-scale operations. They are often equipped with pre-built integration capabilities, industry-specific modules, and support for global compliance standards. However, these solutions may come with high implementation and support costs, making them more suitable for businesses with complex requirements.
- Mid-Tier and Lower-Tier Solutions: These options are typically more affordable and may offer a higher degree of customization. They work well for medium-scale businesses looking for modular solutions or companies planning to augment existing systems with niche functionalities. While they may lack some advanced features, tier-2 or tier-3 solutions can be augmented with third-party tools to create a robust logistics management system.
- Scalability and Flexibility
- As the business grows, the chosen WMS/TMS should be able to handle increased transaction volumes, support expansion into new regions, and integrate with additional systems. Ensure the solution allows easy customization and configuration changes to adapt to evolving business needs without significant disruptions.
- Integration Capabilities
- Seamless integration with other enterprise applications (ERP, CRM, OMS, etc.) is essential. Leading vendors like SAP and Blue Yonder offer well-documented APIs and middleware capabilities for smooth data flow across systems. Custom solutions or mid-tier systems may require additional integration efforts, including the use of middleware tools or custom-built APIs.
- Deployment Options
- Cloud-based solutions (SaaS) are favored for their flexibility, regular updates, and lower upfront costs. They are ideal for businesses that prefer minimal infrastructure management. On the other hand, on-premise or hybrid models may be more suitable for industries with stringent data security requirements, such as financial services or government sectors.
- Cost Considerations
- Analyze the total cost of ownership (TCO), including implementation, licensing, customization, and ongoing support costs. Evaluate not only the one-time costs but also the recurring costs such as subscription fees, support charges, and integration expenses. Top-tier vendors typically have higher initial costs, while lower-tier or in-house solutions can be more budget-friendly but may incur higher costs in the long run due to customization and maintenance.
- Change Management and User Adoption
- Selecting a new WMS/TMS often requires significant change management. The organization must prepare to handle process changes, user training, and potential resistance. A comprehensive change management plan is essential to drive user adoption and ensure a smooth transition.
Industry Trends in WMS and TMS Solutions
- Automation and AI Integration
- Increasingly, automation is being used to handle repetitive tasks, such as sorting, picking, and packaging, while AI-driven algorithms help optimize transportation routes, predict potential delays, and automate decision-making in real time.
- Digital Twins and Simulation Capabilities
- Advanced WMS and TMS solutions incorporate digital twin technology for simulating various logistics scenarios. This allows companies to model warehouse layouts or transportation networks to optimize resource allocation and improve decision-making.
- Unified Platforms with Built-In Analytics
- Many top-tier vendors now provide unified platforms that integrate WMS, TMS, and OMS functionalities into a single solution. Built-in analytics capabilities offer real-time insights, allowing logistics managers to proactively manage inventory, transportation, and fulfillment operations.
Approach to Selecting WMS and TMS Solutions
- Conduct a Thorough Assessment of Current and Future Needs
- Begin by documenting the current processes, systems in use, and pain points. Engage stakeholders across the organization to understand functional requirements and align them with long-term business goals. Identify must-have features such as inventory tracking, automated route planning, and advanced reporting capabilities.
- Consider future growth, regulatory requirements, and technological trends when evaluating these needs. This ensures that the system not only meets current operational demands but also remains adaptable to future changes.
- Evaluate Vendors Using a Comprehensive Scorecard
- Develop a scorecard that compares vendors across multiple criteria, such as functionality, ease of use, scalability, cost, support, and integration capabilities. Gartner or Forrester reports can provide valuable insights into leading solutions like SAP, Blue Yonder, or Infor, while customer reviews and case studies offer practical perspectives on tier-2 and tier-3 options.
- Conduct workshops or pilot implementations with shortlisted vendors to assess how well their solutions align with your business processes. This hands-on approach enables the identification of potential gaps and strengths early on.
- Plan for a Phased Implementation
- Implement the solution in phases to minimize disruptions. Start with a pilot phase that addresses a specific segment of the operation, followed by gradual rollouts to additional sites or departments. This phased approach helps to identify potential issues and ensures that lessons learned can be applied to subsequent phases.
- Data Migration and Integration Planning
- Develop a robust data migration plan to ensure a smooth transition from legacy systems. Use middleware and APIs to facilitate data exchange and synchronization across WMS, TMS, and other systems like ERP or CRM. For highly integrated environments, use enterprise service buses (ESBs) or data virtualization tools to streamline data flow.
Best Practices for Successful WMS and TMS Implementation
- Align Systems with Business Objectives
- Ensure that the selected WMS/TMS solution supports the strategic objectives of the organization. This involves working closely with key stakeholders to map system functionalities to business outcomes such as improved order accuracy, reduced lead times, and cost savings.
- Prioritize Training and User Adoption
- Invest in comprehensive training programs tailored to different user roles. Use e-learning modules, hands-on workshops, and user manuals to help employees get comfortable with the new system. Continuous training ensures that new hires or teams with evolving responsibilities can leverage the system effectively.
- Plan for Organizational Change Management (OCM)
- Pre-Implementation: Communicate the benefits and rationale behind the new system to build buy-in. Involve employees early by seeking their input on system requirements and expected challenges.
- During Implementation: Provide on-site support and user assistance during initial rollouts. Establish a feedback mechanism to address issues promptly.
- Post-Implementation: Regularly review the system’s impact on operations and user feedback. Implement continuous improvement programs to keep the system aligned with changing business requirements.
- Use Real-Time Data and Analytics for Continuous Improvement
- Utilize the analytics capabilities of modern WMS/TMS solutions to monitor KPIs such as order accuracy, inventory turnover, delivery times, and transportation costs. Real-time dashboards enable proactive decision-making and continuous process optimization.
Key Takeaways
- Functionality and Integration: The selected WMS/TMS should support critical logistics functions and integrate seamlessly with existing enterprise systems.
- Vendor Selection Based on Tiers: Evaluate both top-tier solutions like SAP, Blue Yonder, and Infor for comprehensive, integrated platforms, and mid-to-lower-tier options for cost-effective, modular implementations.
- Change Management is Crucial: Implement structured change management practices before, during, and after system deployment to facilitate user adoption and minimize disruptions.
Choosing the right WMS and TMS solution is a strategic decision that requires a well-rounded approach. By considering the factors outlined here and following best practices, organizations can select a system that not only meets their immediate needs but also positions them for long-term success.