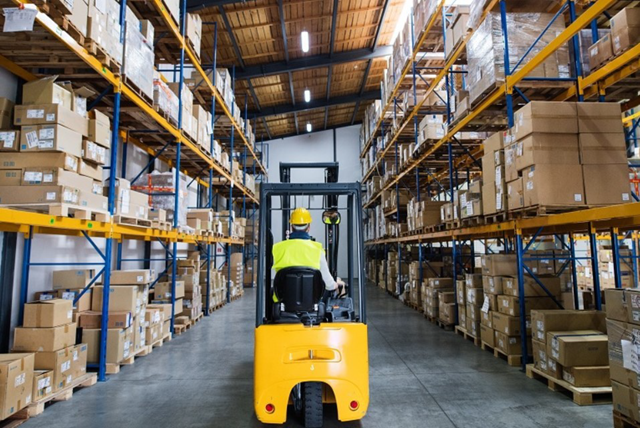
STREAMLINE YOUR WAREHOUSE OPERATIONS AND DRIVE PRODUCTIVITY AND SERVICE LEVEL IMPROVEMENTS
REVAMP WAREHOUSE LAYOUT, BUSINESS PROCESSES, AND SYSTEMS TO OPTIMIZE YOUR WAREHOUSE OPERATIONS
Inefficient Warehouse Operations Impacting Cost and Customer Service
Warehouse operational inefficiencies can impact productivity, safety, service levels and ultimately profits.
- Some of the common challenges faced by warehouse management teams are listed below.
- Warehouse Design: Random storage locations and unclear navigation paths for people and equipment can lead to significant challenges in day to day operations.
- Processes: Key business processes (e.g., pick-up and put-away) are not clearly defined, can lead to significant errors and rework.
- Systems: Lack of automation of key business processes using systems (e..g OMS, WMS) and / or lack of compliance to system usage can affect productivity and service levels.
- People & Equipment: Lack of trained personnel and not having right equipment for moving goods can lead to productivity and safety issues.
Warehouse Optimization for Efficient and Cost-Effective Operations
Our solution approach takes stock of your current warehouse maturity, identifies gaps and recommends a way forward, and implements the recommendations to deliver tangible improvements in a phased manner.
- Our structured assessment leveraging our codified expertise ( critical success factors, templates, checklists and blueprints etc.,), ensures our solution recommendations are tailor made to your unique challenges.
- Step 1: Consult
- We conduct a field study of your warehouse operations by interviewing stakeholders and analyzing various aspects like warehouse layout, business processes, systems, people, equipment and performance metrics.
- We assess maturity of your warehouse operations using 100+ critical success factors and identify gaps and opportunity areas.
- We identify solution recommendations based on critical assessment of gaps and opportunity areas, and the define a roadmap with short-term and long-term priorities.
- Step 2: Implement
- Our implementation approach is a holistic approach addressing multiple aspects
- Warehouse layout design and planogram, racking system and equipment
- Process Re-engineering: Product / Item profiling and storage policy, inbound and outbound process optimization, inventory management policies and cycle count, metrics and KPIs
- Systems Implementation/upgrades (OMS, WMS, TMS) to automate the re-engineered processes
- Our implementation approach is a holistic approach addressing multiple aspects
- Step 1: Consult
Quantifiable Improvements to Productivity and Service Levels
Our solution and consulting approach delivers quantifiable improvements on all aspects – safety, productivity and customer satisfaction.
- Our structured approach to improving your warehouse operations yields the following quantifiable benefits
- Enhanced inventory visibility: Real-time data on inventory levels and locations allows for faster replenishment and better stock control.
- Improved labour productivity: Efficient task allocation and workload distribution among workers reduce idle time and maximize productivity.
- Better workplace safety: Optimized warehouse layouts reduce congestion, streamline workflows, and ensure proper handling of equipment and materials, minimizing accidents and injuries.
- Improved Picking efficiency and accuracy: Streamlined picking processes reduce travel time and errors, increasing the speed and accuracy of order picking.
- Faster Turnaround Time: By improving processes, warehouses can handle more throughput in less time, leading to faster processing of incoming and outgoing goods.
- Reduced Delivery Errors and Damages: Efficient packaging and material handling processes minimize the chances of product damage during shipping, improving the quality of goods delivered and minimizing returns.
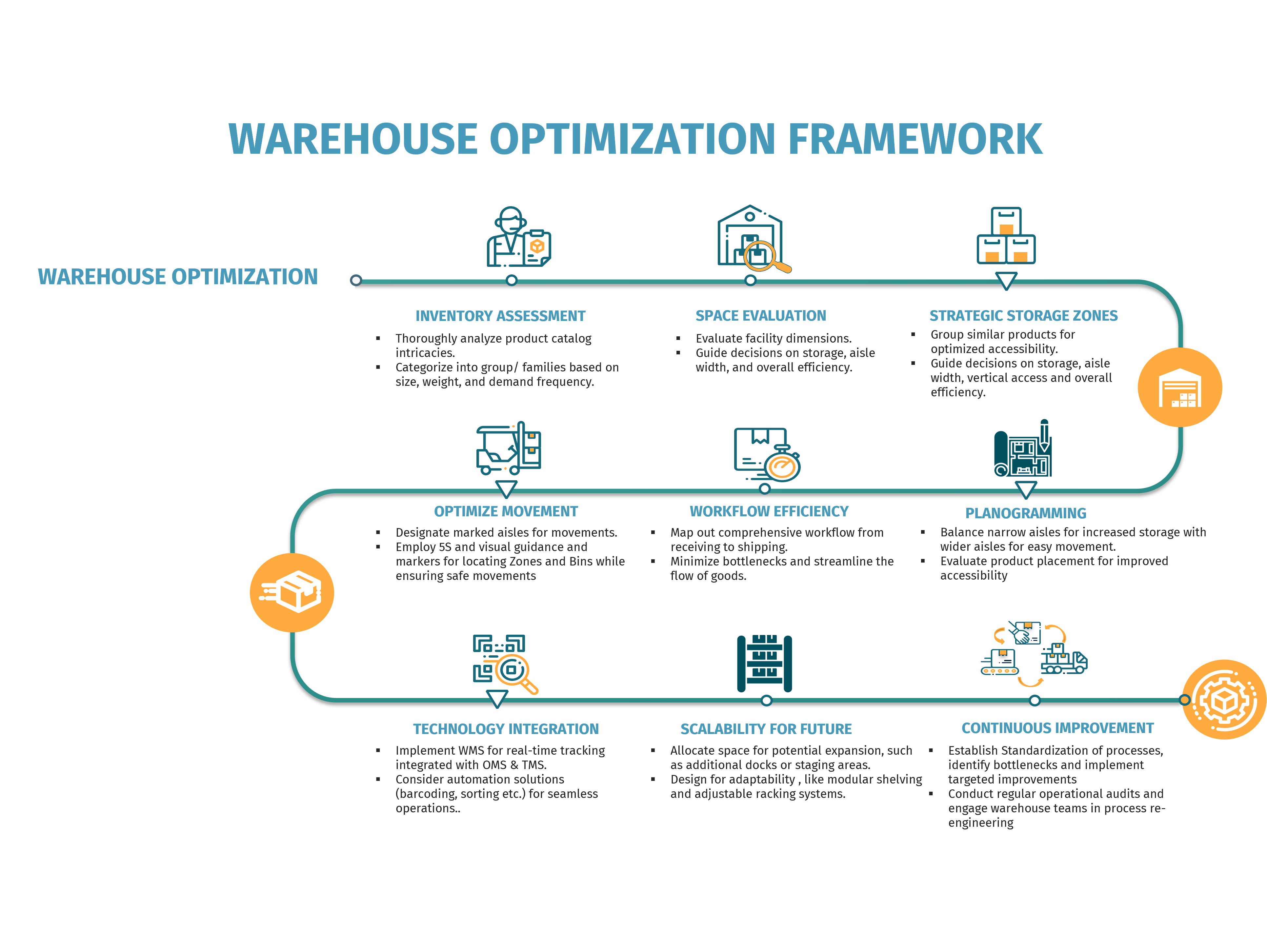